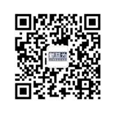
微信公眾號二維碼

微信咨詢顧問二維碼
精益生產(chǎn)管理咨詢公司國內(nèi)大盤點?新益為精益生產(chǎn)管理咨詢公司概述:在制造企業(yè)追求高質(zhì)量發(fā)展的今天,精益思想作為一種全局優(yōu)化的管理方式,已被越來越多企業(yè)所重視。它不僅聚焦于流程效率的提升,更強調(diào)全員參與、持續(xù)改善、客戶價值最大化等理念。在實際推進過程中,許多企業(yè)發(fā)現(xiàn),僅靠內(nèi)部力量難以深入實施。此時,借助專業(yè)的精益生產(chǎn)管理咨詢公司,成為一種高效、系統(tǒng)的路徑選擇。
精益生產(chǎn)管理咨詢公司
“精益生產(chǎn)”的核心在于消除一切浪費,通過構(gòu)建流暢、可視、標準化的作業(yè)流程,提高交付速度、降低庫存、穩(wěn)定品質(zhì)。雖然理論成熟,但落實到不同類型的工廠卻極具差異性。例如,汽車零部件企業(yè)的瓶頸可能在于換線效率,食品加工廠則需解決批次轉(zhuǎn)換和衛(wèi)生標準沖突,電子制造則面臨多批次、小訂單的快速響應問題。此類問題都要求經(jīng)驗豐富的精益生產(chǎn)管理咨詢公司介入,進行現(xiàn)場調(diào)研、流程診斷與定制化方案設計。
與傳統(tǒng)培訓或管理外包不同,精益生產(chǎn)管理咨詢公司更傾向于“陪伴式”“教練式”的服務方式。他們通常通過以下幾個步驟推進改善:第一,深入一線調(diào)研數(shù)據(jù)與流程,梳理價值流并識別浪費環(huán)節(jié);第二,結(jié)合工廠發(fā)展目標,制定符合實際的改善計劃;第三,引導管理層與一線員工共同參與,推動作業(yè)標準化、現(xiàn)場目視化、物料流動化等關(guān)鍵動作;最后,逐步建立PDCA機制,使改善成為文化,融入企業(yè)日常運行體系。
在過去的實際案例中,不少企業(yè)通過精益生產(chǎn)管理咨詢公司的輔導,獲得了顯著的經(jīng)濟效益。某中型機械制造廠原先庫存積壓嚴重,缺料頻繁,計劃體系幾近失效。咨詢團隊介入后,通過價值流分析重建了整個拉動式生產(chǎn)計劃機制,并在車間內(nèi)導入看板管理、同步化流程、快速換模機制。半年內(nèi)庫存降低約40%,物料齊套率提升至95%以上,客戶交期達成率從原先的70%提升至98%。
當然,選擇一家合適的精益生產(chǎn)管理咨詢公司也并非易事。當前市場上咨詢機構(gòu)眾多,水平良莠不齊。有些公司更側(cè)重于講授工具,有些則擅長系統(tǒng)落地與組織變革。有的咨詢公司僅適用于單一行業(yè),有的則能覆蓋多個工業(yè)門類。企業(yè)在選擇時,應重點考察以下幾點:是否具備可驗證的成功案例?顧問團隊是否有真實制造業(yè)經(jīng)驗?是否能夠融入企業(yè)文化并帶動員工積極性?是否能推動可持續(xù)改善機制的建立?
未來,隨著工業(yè)智能化的深入發(fā)展,精益生產(chǎn)管理咨詢公司的角色也在持續(xù)演變。不少咨詢公司已將數(shù)字化轉(zhuǎn)型、MES系統(tǒng)、工業(yè)物聯(lián)網(wǎng)等融入精益路徑中,探索“數(shù)字精益”的新方向。通過將實時數(shù)據(jù)監(jiān)控與現(xiàn)場作業(yè)連接起來,實現(xiàn)對浪費的快速識別、對瓶頸的自動預警,以及對流程優(yōu)化的持續(xù)支撐。這種趨勢意味著,未來的精益不僅僅是流程優(yōu)化,更是一種智慧制造的整體思維。
總而言之,精益不僅是一種改善工具,更是一種理念、一種文化。而推動這一文化深植企業(yè)的土壤,離不開專業(yè)的精益生產(chǎn)管理咨詢公司。在市場競爭愈發(fā)激烈、客戶需求不斷變化的時代背景下,企業(yè)唯有構(gòu)建快速反應、持續(xù)優(yōu)化的運營體系,才能在動蕩中求穩(wěn),在穩(wěn)定中謀進。借助一家專業(yè)的精益生產(chǎn)管理咨詢公司,不僅是提升當前效益的選擇,更是面向未來競爭力的長期投資。
精益生產(chǎn)管理咨詢公司國內(nèi)大盤點?以上就是新益為精益生產(chǎn)管理咨詢公司的相關(guān)介紹,做好企業(yè)的精益生產(chǎn)管理咨詢工作就是為精益生產(chǎn)活動打下基礎(chǔ),讓精益生產(chǎn)管理在企業(yè)發(fā)展中有一個良好的發(fā)展前提。
文章來源于網(wǎng)絡,版權(quán)歸作者所有,如有侵權(quán)請聯(lián)系刪除
建立生產(chǎn)有序、管理順暢,操作規(guī)范,士氣高昂、高質(zhì)量、低成本、短交期的作業(yè)現(xiàn)場;
為企業(yè)規(guī)劃設計一套由內(nèi)到外的形象升級,外觀視覺價值體現(xiàn)、內(nèi)在的管理內(nèi)涵體現(xiàn);
全員參與設備管理高產(chǎn)出和低成本運營,提升設備管理能力,維護能力,提高效率
構(gòu)建班組生產(chǎn)管理體系、循環(huán)評價、人才育成、持續(xù)改善、績效管理、文化養(yǎng)成體系;
提高產(chǎn)品質(zhì)量、降低生產(chǎn)成本、縮短交期、增加利潤,讓管理更系統(tǒng)科學,執(zhí)行力更強
對工廠的各個組成部分進行合理安排,以提高生產(chǎn)效率、降低成本、優(yōu)化物流、改善工作環(huán)境等